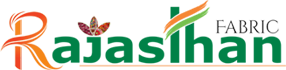
Split ply camel girths of Rajasthan are generally made manually by hand without involving any sort of loom. Goat hair or cotton cord is woven into yarn on the spindle which is then doubled to make it two-ply and so on. A four-ply yarn is used for girth, with each ply being two-ply. Black and whie yarn.The dry four ply yarn is spooled on a spindle and the cords of one of the cords is split open with the eye end of a large wooden needle and untwisted to a quarter of a turn";" the next cord is threaded through the eye and is pulled back through the first strand. The process is done along the row, and worked down, row by row, where each individual cord reaches down and across the newly created fabric on a diagonal line ending on the selvedge, finally creating a zigzag pattern. There are standard variations in pattern, which could either be monochrome, chequered, or a pattern in horizontal waves.
“High-twist cords are essential for Ply Splitting. They are not readily available to buy, so it is common to make your own. Traditionally, they were made from hand spun goat hair, but smooth cotton, linen, silk, rayon or rug yarn all work as well.” The ideal tool for Ply Splitting is the grip fid, which is available in various diameters and in which the tube size is chosen to match the diameter of cords in use. Alternately, a rug latchet hook may be used; the disadvantage of this tool is that it harder to draw the doubled cord (splitter) through the splittee.
During the 90s, Peter Collingwood travelled to India and collected and analysed braided artefacts, the techniques of which had been barely documented before him. His research culminated in a book ‘The Techniques of Ply Split Braiding’, published in 1998. Consequently, weavers and braid makers have explored and developed it in a number of directions. Textiles, jewellery, bags, belts, hats and even dresses have been developed by some makers, while others have taken the technique to create three-dimensional vessels, baskets and sculpture.